HSK (German and Italian Hohl Schaft Kegel abbreviation) tool handle is a kind of double-sided clamping tool handle developed by the Institute of Machine Tool Research of Aachen University of Technology in Germany in the early 1990s. It is the most representative double-sided clamping tool handle. Since 1987, it has been manufactured by WZL, the Institute of Machine Tool Research of German University of Technology, and some tool manufacturers and machine tools manufacturers. More than 30 units, such as factories and user enterprises, have set up thematic working groups to start the research and development of new tool systems under the leadership of Professor M. Weck. After the Toronto study, the working group submitted to the German National Standard Machine Tool Organization in July 1990 the standard proposal of "automatic change/j tranquil handle". In July 1991, Germany released the DIN standard of HSK tool system for the record, and proposed to ISO to formulate relevant ISO standards. In May 1992, ISOTfrC29 (Tool Technical Committee) of the International Organization for Standardization (ISOTfrC29) decided not to establish the ISO standard for automatic replacement/J hollow handle for the time being. After the second round of study by the working group, Germany formulated the formal industrial standard DIN69893 for HSK tool system in 1993. In May 1996, under the ISO/TC29/WG33 Review Conference, the draft ISO/DISl2164 standard for HSK plant-only system based on DIN69893 was formulated. After many revisions, the formal ISO standard IS012164 of HSK tool system was promulgated in 2001. Because of its stiffness and repetitive positioning accuracy several to several dozen times higher than that of standard taper TOOL HOLDER, it has been widely recognized and adopted in the mechanical manufacturing industry. For example, HSK/J shank is widely used in milling, drilling and turning at Benz Motor Company and Volkswagen Motor Company in Germany. Hsk Tool Holder is positioned on both sides of cone (radial) and flange (axial), and the machine tool is rigidly connected with the spindle. When the tool shank is installed on the spindle of the machine tool, the hollow short taper shank can fully contact with the taper hole of the spindle and play a centring role. At this time, there is a gap of about 0.1 mm between the flange of HSK tool shank and the end face of the spindle. Under the action of the tension mechanism, the backward movement of the tie rod causes the conical surface of the front end to expand the elastic claw radially. At the same time, the outer conical surface of the claw acts on the 30-degree conical surface of the inner hole of the hollow short conical handle. The hollow short conical handle produces elastic deformation, which makes the end face of the tool and the end face of the spindle close to each other, and realizes simultaneous determination of the tool handle and the conical surface of the spindle and the main gla Bit and clamping function. The main advantages of this tool handle structure are as follows: (1) Effectively improve the stiffness of Tool Holder and machine tool spindle. The effective contact area between the tool handle and the spindle is enlarged due to the combination of conical and end-face over-positioning, and the combination stiffness between the tool handle and the spindle is greatly improved by double-sided positioning from both radial and axial directions, which overcomes the weakness of the traditional standard taper handle when rotating at high speed. (2) It has high repetitive positioning accuracy and fast automatic tool change, which is conducive to the realization of high-speed ATC. Because of the taper used, the taper length is shortened (about I/2 of the taper handle with similar specifications). The contact area between the handle and the spindle of each tool change is large, which makes the machine tool better and improves the repetitive positioning accuracy of the handle. Because of the hollow structure, it is light in weight and easy to change knives automatically. (3) It has good high-speed locking performance. The elastic expansion claw is locked between the tool handle and the spindle. The higher the rotational speed, the greater the centrifugal force of the expansion claw and the greater the locking force. According to German DIN standard, HSK/J handle adopts balanced design. Its structure forms are A, B, C, D, E and F. Each type has a variety of sizes and specifications. Types A and B are automatic tool changers, C and D are manual tool changers. Types E and F are keyless connecting tool holders, which are suitable for ultra-high speed cutting.
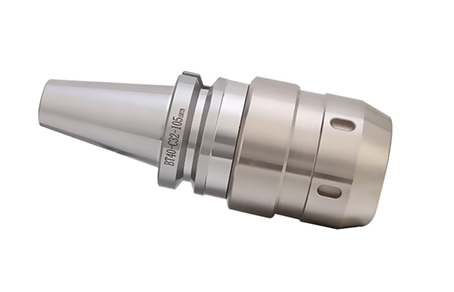